中間包用耐火材料及耐火噴涂料對潔凈鋼的作用
發(fā)布時間:2022/2/7 18:45:01 點擊率: 來源:高鋁磚廠家 作者:榮盛耐材中間襯里一般由保溫層、中間層和工作襯里組成。保溫層采用粘土磚或保溫板,中間層一般采用低水泥或超低水泥澆注料,氧化鋁含量為60%-80%。工作襯里應滿足以下條件:
(1)耐鋼水和熔渣侵蝕,使用壽命長;
(2)抗熱震性能好,與鋼水接觸時不爆裂;
(3)熱傳導率低,熱膨脹小,使中間包襯具有一定的保溫性和良好的完整性;
(4)澆注過程中不污染鋼水;
(5)易于砌包和拆卸。
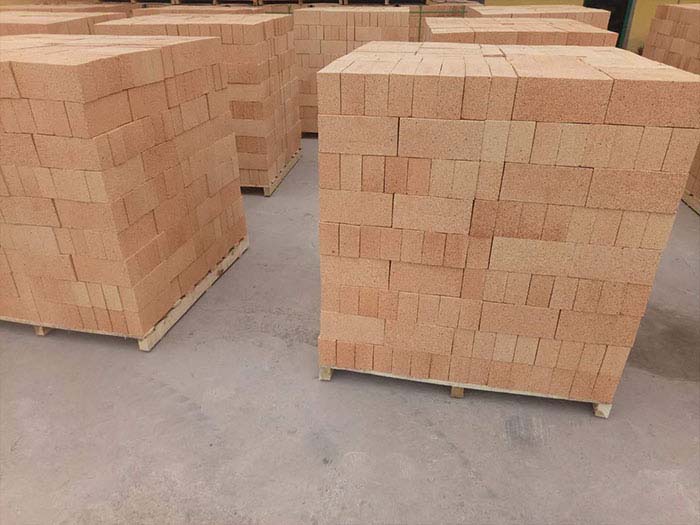
中間包襯主要由以下部分組成:
(1)保溫層。
該層緊鄰中間包鋼殼,其材料通常為石棉板、保溫磚或輕質澆注料。
(2)中間層。
該層與保溫層接觸,其材料一般為粘土磚。
(3)工作層。
與鋼水接觸的一層是工作層。本層內襯材料主要包括:高鋁磚、堿性磚(如鎂磚等)、硅保溫板、鎂保溫板、鎂橄欖石保溫板及涂料,如鎂、鎂鉻涂料等。
中間包內襯也有澆注料。
(4)座磚
鑲嵌在中間包底,安裝中間包水口。其材料一般為高鋁。
(5)包底
中間包底,其材料與工作層基本相同。
(6)包蓋
中間蓋,復蓋在中間包上,可以起到保溫和防止鋼水飛濺的作用,其材料通常由粘土磚或澆注料制成。
(7)擋渣墻。
墻建在中間包里,可以是單墻,也可以是雙墻。單墻或雙墻擋渣墻,顧名思義,其目的是擋渣,以提高鋼水的清潔度。還可以設置鋼水過濾器,進一步去除鋼水中的雜物。擋渣墻的材料通常是高鋁的,可以用磚砌在中間包里,也可以做成預制塊,放在中間包里。
中間包主要有:
(1)高溫中間包。
中間包是為特定的冶金工藝設置的,包襯采用鎂磚,預熱至1500℃左右。
(2)熱中間包。
也就是說,目前鋼廠常見的中間包是燒磚或不燒磚或澆注料的中間包。澆筑前預熱至800~1100℃。
(3)冷中間包。
采用保溫板作為襯里,澆筑前不經預熱即可使用。
至于選擇哪種中間包類型和哪種材料作為襯里,這取決于澆筑鋼種、冶煉方法、烘烤條件和鋼廠本身的能力。
耐火材料擋渣墻在煉鋼中間包工作層的性能優(yōu)勢
煉鋼中間包擋渣堰系列耐火材料:沖擊板、擋渣堰材料、理化指標、優(yōu)缺點,以及鋼水流量對中間包的影響。
鋼水的理論停留時間是中間包容量和中間包鋼水流量的鋼水停留時間,但中間包鋼水流量不均勻,有些地方快,有些地方慢,特別是中間包底部有不活躍的鋼水停滯區(qū),夾雜物難以上浮。鋼水在中間包中的實際平均停留時間比理論上的平均停留時間短。為充分有效利用中間包容積,促進夾雜物上浮,采取措施在中間包中增加擋土墻和大壩,目的是:
1.消除中間包底部的死區(qū);
2.改善鋼水流動軌跡,使流動沿鋼渣界面流動,縮短夾雜物上浮距離,有利于渣的吸收;
3.將鋼包注流沖擊引起的強渦流限制在局部區(qū)域,防止紊流擴散引起表面波,將渣子卷入鋼水中。
試驗指出,中間包使用擋渣墻和壩后,鋼的清潔度提高了。無擋渣墻板坯表面鋁酸鹽夾雜2.9%,加擋渣墻2.1%。使用擋渣墻和壩,板坯表面夾雜從2.1%降至0.3%。
鎂擋渣墻的優(yōu)點擋渣墻主要由鎂、高鋁和尖晶石制成。鎂擋渣墻的優(yōu)點如下:
1.抗熱震性能好;
2.在工作溫度下具有佳的熱強度;
3.浸泡在鋼水中,PO2含量低時強度高;
4.帶入鋼水的氧含量較低,比高鋁擋渣墻少80%;
5.吸收夾雜物中的Al2O3,在擋渣墻表面形成尖晶石;
6.低成本。
目前使用的中間包工作包括涂料、保溫板、干振動料等。
中間包涂料包括鎂、鎂鉻和鎂鈣。特別是鎂鈣涂料不僅對鋼水和鋼渣具有較高的化學穩(wěn)定性,而且具有凈化鋼水的作用,在大型鋼袋中使用效果良好。
目前,MgO和MgO-CaO耐火噴涂通常以FS為組合劑。由于FS粒度非常細(大部分小于1μm),活性高,容易在水中形成Si-OH結構,可形成=Si-O-H+。對于MgO耐火噴涂,即在MgO-SiO2-H2O系統(tǒng)中,會發(fā)生以下反應:
上述一系列反應可在常溫下發(fā)生,使噴涂層硬化,具有較高的常溫強度。反應式4-8形成的網狀結構不隨熱處理溫度的升高而分散。反應式4-10和反應式4-11生成的3Mgo.4SiO2.H2O和3Mgo.2SiO2.2H2O可在900℃左右轉化為2Mgo-SiO2組合相,使噴涂層產生較高的中溫強度。這就是為什么FS組合的MgO耐火噴涂層在整個溫度范圍內具有較高的強度。
FS組合的MgO-CaO質耐火噴涂,首先形成的含水MgO-SiO2組合相,在烘烤和使用過程中會逐漸轉化為2cao-SiO2和3cao-SiO2組合相,并與MgO-CaO相直接結合,提高MgO-CaO質耐火噴涂的高溫性能。
濕噴涂料在中間包的應用
同時具備中間包應用條件的堿性耐火噴涂主要包括MgO質量、2MgOSiO2/MgOSiO2-MgO質量和MgO-CaO質量。目前常用的是MgO質量,其MgO含量大于85%;其次是2MgOSiO2/2MgOSiO2-MgO質量,MgO含量通常大于60%。為了進一步提高冶金效果,選擇MgO-CaO質量,其CaO含量不小于8%。各種堿性耐火噴涂均為普通、優(yōu)質、保溫三系列。
Mgo以燒結鎂砂或電熔鎂砂為主要原料,Mgo不小于90%,好Mgo不小于95%。
2MgOSiO2/2MgOSiO2-MgO以鎂橄欖故石為主要原料,為提高耐久性,可配入一定量的鎂砂。
MgO-CaO以CaO材料為主要原料(主要是骨料),以鎂砂為細粉(基質)。
鎂鈣耐火噴涂料對潔凈鋼的作用
Mgo-CaO耐火噴涂可以用來說明減少鋼中混合物的影響。我國幾家大板坯連鑄鋼廠拉速普遍較快。使用保溫板時,第一爐氣泡廢品率高達30%,開澆率只有80%左右。使用Mgo-CaO耐火噴涂后,對板坯進行抽樣檢查,未發(fā)現(xiàn)氣泡廢品,開澆全部成功。
通過對實驗室試驗結果和噴涂現(xiàn)場實際使用后情況的分析,我們可以看到,在澆鋼過程中,MgO-CaO耐火噴涂料吸附鋼水中的AI2O3.SiO2.Fe2O3等夾雜物與自身反應燒結。隨著澆鋼時間的增加,鋼水中的各種夾雜物逐漸進入涂層,導致涂層本身的CaO/SiO2比發(fā)生變化。
從比較統(tǒng)計數(shù)據(jù)來看,Mgo-CaO耐火噴涂澆筑普通碳鋼硅酸鹽夾雜物的大直徑遠小于硅質保溫板的中間包裝,開澆第一爐鋼時操作順利,撈渣少,開澆率100%。鑄造硬線鋼時,粗硅酸鹽混合比例遠低于硅質保溫板中間包裝。從Mgo-CaO耐火噴涂在各鋼廠的應用實踐結果來看,Mgo-CaO耐火噴涂對鋼水的清潔效果明顯,與傳統(tǒng)的硅質保溫板和Mgo耐火噴涂相比具有很大的優(yōu)勢。隨著我國連鑄比例的不斷提高。隨著品種鋼尤其是特種合金鋼比例的增加,鋼材質量尤其是清潔度的要求越來越高。估計這種堿性耐火噴涂料將得到廣泛應用。
如何提高中間包的使用壽命
連鑄中間采用上水口,傳統(tǒng)形狀為喇叭直通形,鋼流控制靠塞棒和喇叭形上水口接觸線進行調整。隨著鑄造時間的延長,喇叭形上水口的鋼口和塞頭不斷腐蝕,導致吻合不嚴,鋼水失控,停止鑄造。同時,由于直徑擴大,上水口出口失控,嚴重時會造成事件。
某廠將上水口的喇叭形接鋼口改為球面碗形漏斗擴張形接鋼口。因此,當水口與塞棒配合時,由原來的線接觸改為球面接觸,增加了封閉面積,使其很好地匹配和控制鋼流。由于漏斗膨脹,漏斗柄起到定徑水口的作用,通過膨脹部位的鋼水旋轉成渦流進入結晶器,使進入結晶器的鋼水溫度分布均勻,減少鋼坯形成中的裂紋和脫口,提高鑄坯質量。同時,工廠將上水口和下水口的錐形工作段改為等徑柱工作段。即使上水口頭部失去功能,工作段仍能有效控制鋼水,穩(wěn)定鑄造和關閉,使出水口具有雙重保險功能。材料方面,工廠將上水口球面碗形漏斗和下水口的等徑柱段由普通材料改為特殊材料,即成為復合水口,提高了水口的耐沖刷性和耐腐蝕性。
復合出水口用于鋼鐵總廠煉鋼矩形坯。鑄造20mnsi鋼的爐數(shù)由2-3爐增加到12-I3爐,連鑄時間由2h增加到10h,效果明顯,大大提高了中間包的使用壽命。